
By Gordon
Rayner (President of California Pavement Maintenance, Inc.)
February
2009
The first project I did at San Francisco
International (SFO) was 31 years ago in 1977. That was installing a
fuel-resistant coal tar sealcoat on a large aircraft parking ramp at the
International Terminal. Thirty years later we received a request that
had a familiar ring to it; SFO needed a safe, fuel-resistant protective
coating for parking ramps, refueling and taxiing areas at the
International Terminal.
San
Francisco International, one of the busiest airports in the world, is
located on land that extends out into the San Francisco Bay and is
naturally very environmentally sensitive. Coal tar would no longer be an
option.
The challenge required a new approach to protective
coatings and that challenge was given to Carbonyte Systems, Inc. of
Sacramento.
The material to be used for the SFO Plot 3 Tarmac
area needed to be a cold process, aggregate filled material that would
meet ASTM D 2939 standards for fuel resistance. ASTM D 2939 is the
current transitional standard for the FAA on fuel-resistant pavement
sealers.
Bill Coe, research technologist with Carbonyte
Systems, drew on years of asphalt sealcoat formulation experience for
the base design of asphalt binders, crushed aggregates and polymers but
new innovation was necessary to meet D 2939. For this he turned to Earth
Resin(tm), a product developed by Prime Plex LLC(tm).
Earth Resin(tm) begins as a conventional, 20 mesh
ground tire rubber which is deploymerized to a fine, cross-linkable
black powder by a technology know as the P2GTR(tm) permutation process.
During the cross-linking process, select virgin elastomers are grafted
into and interwoven with the rubber to create a broad range of positive
performance characteristics. The performance characteristics necessary
for the Plot 3 Tarmac project were: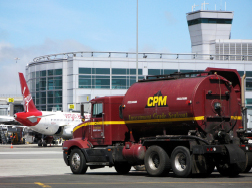
1.
Non-toxic, non-carcinogenic
2.
Non-polluting, no pah's, no hap's and negligible voc's
3.
Safe to handle and store, container residue landfill safe
4.
Persistent curing in cool temperatures
5.
Superior fuel and water resistance.
6.
Dries insoluble with crosslink additive
Bill coordinated with Prime Plex(tm) for the
processing of the Earth Resin(tm); proposed project material samples
were made and lab tests were run for compliance. With a final mix
design in hand for CarbonSeal-FR, two test strips were placed for
evaluation on Plot #3 in November of 2007.
The
two sections selected straddled the area where 777's, some weighing
more than 400,000 lbs., would travel and would allow approving engineers
to monitor the CarbonSeal-FR's performance under heavy traffic and
torsional loads.
Approval came in January of 2008 but, with fog
being very prevalent during the winter at SFO we had to wait for a break
in the weather to proceed. In April a clear stretch of dry weather was
forecast and the project was set in motion. Application specifications
called for two coats of material; the first to be squeegee applied and
the second to be spray applied. For application Bill turned to
California Pavement Maintenance Company and a new PavementSaver sealcoat
machine which could both squeegee and spray.
Weather conditions on April 8th were cool, clear
and very windy but before any work could be done we had to clear
security. Security at any International Airport is strict but bringing
equipment onto active airport taxi and parking areas requires thorough
equipment and personnel inspection. Despite having submitted all the
four man crew's personal information and description, equipment
registrations and serial numbers and MSDS's for all our materials,
bringing material on-site in a big tank seemed to create additional
problems so the San Francisco police department was called in to assist
airport security. What we didn't know at the time was the Olympic Torch
was due to arrive and depart while we were there working and security
was extra tight.
On-site,
several hours late, we had to finish cleaning the work area. Airports
keep their taxi areas very clean and SFO is no exception so we were
simply assuring there was no loose sand or other wind-blown items on our
work area. Once clean, the application of CarbonSeal-FR began with
cutting the material 15% and proceeding to squeegee the first coat.
Working on an active airport ramp, as it turned
out, meant working on an active airport ramp! The crew was a little
shocked when 747's came rolling by, their huge size making them seem to
be right next to them, their wings seemingly going over their heads.
By the end of the day the crew had placed two coats
on 100,000 square feet. Curing, despite cool temperatures and the close
proximity to the salt water, was fairly quick due to help from the high
wind. The wind did cause a small problem in that we had to squeegee both
coats for fear of getting overspray on any aircraft passing by. It was
at the end of day one that we discovered what all the security was
about.
The
Olympic Torch was flown in that day and made its way to the City of San
Francisco where demonstrations disrupted the planned run. A secret
course for the return run to SFO was chosen to avoid the demonstrations
and the Torch made its way back to the airport the next day and flew off
to their next stop in Buenos Aires. With this high profile activity at
SFO it became apparent to us that the facility managers had confidence
in both who we were and what we were doing on the flight line.
Day two went much smoother, security knew who we
were and we arrived on-site on time and ready to go. The weather was
still clear but also very windy as two coats were placed on an
additional 200,000 square feet. Spraying was accomplished on a small
area well away from the airplanes but the decision was made to squeegee
most of the second coat on day two as well.
Reflection
always allows for 20/20 vision and looking back at this challenge it is
apparent that a number of factors could easily have gone haywire and
caused delays or worse problems. To have a successful ending to a
project that required the development of a new material with unique
strengths and curing abilities and the professional installation that
was required under demanding conditions is a testament to the people and
equipment involved. This project depended on the dedication of Bill Coe
and the entire Carbonyte Team, the support of Prime Plex(tm), the
installation work of CPM and the dependability and production
capabilities of the PavementSaver which was able to handle a highly
rubber modified material with apparent ease.
Success for us is measured in both project
completion and long term material performance. This was the first use of
an asphalt-based, fuel resistant sealcoat that I am aware of and the
installation went off as smoothly as could be wished for. As for
long-term performance, lab trials indicate positive results and recently
Robert Gray (SFO - Facilities, Civil Engineer Dept.) reported that, upon
the January inspection, fuel spills in the area have not penetrated into
the underlying HMA and the coating is holding up well. True to his
nature, Bill kept samples of the actual material used on the project and
sent it to an independent lab for compliance verification. The material
met the ASTM D 2939 standards.
Material development is an ongoing process; each
newly designed material that succeeds leads you into a new field with
new potentials. Continued work on the rubber and curing components used
on the SFO project has led to new discoveries that made their first
appearance at John Wayne Airport in Orange County where an ARB emulsion
was used to seal 640,000 square feet of pavement in the middle of the
night in fog, successfully.
The future of new generation materials is here.

|